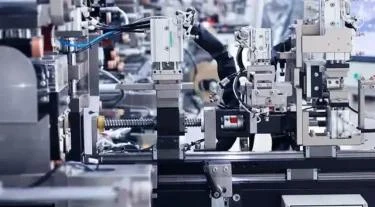
,字数在1000字左右
# Tape Production Process and Techniques
## Introduction to Tape Manufacturing
Tape manufacturing is a complex process that involves multiple stages of production to create adhesive products for various applications. From everyday household uses to industrial applications, tapes serve numerous purposes in our daily lives. The production process combines material science, chemical engineering, and precision manufacturing techniques to create reliable adhesive products.
## Raw Materials in Tape Production
The foundation of tape manufacturing begins with selecting high-quality raw materials. The primary components include:
– Backing material (paper, plastic, cloth, or foil)
– Adhesive compounds (rubber-based, acrylic, or silicone)
– Release coatings (for easy unwinding)
– Additives (for UV resistance, flame retardancy, etc.)
Each material is carefully chosen based on the intended application of the final product, whether it’s for packaging, electrical insulation, medical use, or industrial purposes.
## The Tape Manufacturing Process
### 1. Backing Material Preparation
The first step involves preparing the backing material. For plastic tapes, this typically means extruding polymer resins into thin films. Paper and cloth backings undergo special treatments to enhance strength and durability. The backing material is wound onto large rolls called “jumbo rolls” that can be several feet wide.
### 2. Coating Process
There are three primary coating methods used in tape production:
– Solvent-based coating: The adhesive is dissolved in a solvent before application
– Water-based coating: Uses water as the carrier for the adhesive
– Hot melt coating: The adhesive is applied in a molten state without solvents
The coating process requires precise control of temperature, viscosity, and application thickness to ensure consistent quality.
### 3. Drying and Curing
After coating, the material passes through drying ovens to remove solvents or water. For certain adhesives, curing under UV light or heat may be necessary to achieve optimal bonding properties. This stage is critical for developing the tape’s final performance characteristics.
### 4. Lamination (for multi-layer tapes)
Some specialty tapes require additional layers for specific properties. Lamination combines different materials to create composite tapes with enhanced features like moisture resistance or increased strength.
### 5. Slitting and Rewinding
The large coated rolls are then slit into narrower widths according to product specifications. Precision slitting machines use sharp blades to cut the material without creating rough edges. The slit rolls are then rewound onto smaller cores for packaging.
### 6. Quality Control and Testing
Throughout the manufacturing process, quality control measures ensure the tape meets specifications. Tests may include:
– Peel adhesion tests
– Shear strength measurements
– Temperature resistance evaluations
– Visual inspections for defects
## Advanced Tape Manufacturing Techniques
Modern tape production incorporates several advanced techniques:
### 1. Precision Coating Technologies
New coating methods like microgravure and slot die coating allow for ultra-thin, uniform adhesive layers with minimal waste. These techniques are particularly valuable for high-performance tapes used in electronics and medical applications.
### 2. Nanotechnology in Adhesives
Incorporating nanomaterials into adhesive formulations has led to tapes with exceptional properties such as:
– Improved thermal conductivity
– Enhanced electrical insulation
– Superior bonding to difficult surfaces
### 3. Environmentally Friendly Production
Many manufacturers are adopting greener practices:
– Water-based adhesives replacing solvent-based systems
– Biodegradable backing materials
– Energy-efficient drying systems
– Recycling programs for production waste
## Specialty Tape Production
Certain tapes require specialized manufacturing processes:
### 1. Double-Sided Tapes
These involve coating adhesive on both sides of a carrier material, often with a release liner to protect one side until use. The production requires precise alignment and tension control.
### 2. Foam Tapes
Incorporating foam layers between adhesives creates tapes with cushioning properties. The manufacturing process must maintain the foam’s cellular structure while ensuring proper bonding.
### 3. Conductive Tapes
Keyword: tape manufacturing