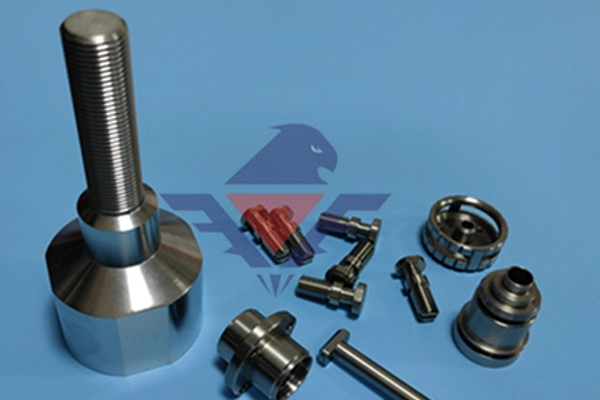
# Precision Swiss Machining for Complex Components
## The Art of Swiss Machining
Swiss machining represents the pinnacle of precision manufacturing, offering unparalleled accuracy for complex components. This specialized machining technique originated in Switzerland’s watchmaking industry, where extreme precision was required for tiny, intricate parts. Today, Swiss machining has evolved to serve industries ranging from medical devices to aerospace and beyond.
## Why Choose Swiss Machining?
The Swiss machining process stands out for several key advantages:
– Exceptional precision with tolerances as tight as ±0.0001 inches
– Ability to machine complex geometries in a single setup
– Superior surface finishes that often eliminate secondary operations
– Efficient production of small, delicate parts that would be challenging with conventional methods
– Reduced material waste through optimized machining processes
## Applications Across Industries
Swiss machining has found applications in numerous industries where precision is paramount:
### Medical Device Manufacturing
The medical industry relies heavily on Swiss machining for components like bone screws, surgical instruments, and implantable devices. The ability to work with biocompatible materials like titanium and surgical-grade stainless steel makes Swiss machining indispensable in this field.
### Aerospace Components
Aircraft and spacecraft demand components that meet rigorous standards for precision and reliability. Swiss machining produces critical parts such as fuel system components, sensor housings, and avionics connectors with the required accuracy and repeatability.
### Electronics and Microtechnology
As electronic devices continue to shrink, Swiss machining provides the solution for manufacturing miniature connectors, pins, and other micro-components essential for modern electronics.
## The Swiss Machining Process
The Swiss machining process differs from conventional CNC machining in several important ways:
– The workpiece is supported very close to the cutting tool by a guide bushing, minimizing deflection
– Tools approach the workpiece radially rather than axially
– Multiple tools can work simultaneously on different sections of the part
– The machine can perform turning and milling operations in one setup
This unique approach allows for the production of long, slender parts that would be impossible to machine accurately using traditional methods.
## Material Capabilities
Swiss machining centers can work with a wide variety of materials, including:
– Metals: Stainless steel, titanium, aluminum, brass, and exotic alloys
– Plastics: PEEK, Delrin, Ultem, and other engineering plastics
– Composites: Various reinforced materials for specialized applications
The ability to machine such diverse materials makes Swiss machining suitable for virtually any precision component requirement.
## Quality Assurance in Swiss Machining
Reputable Swiss machining providers implement rigorous quality control measures:
Keyword: Swiss Machining
– In-process inspection using advanced metrology equipment
– Statistical process control to maintain consistency
– Comprehensive documentation and traceability
– Compliance with industry-specific standards (ISO, AS9100, etc.)
These measures ensure that every component meets the exacting specifications required by today’s demanding applications.
## Choosing a Swiss Machining Partner
When selecting a Swiss machining provider, consider these factors:
– Experience with your specific industry and component types
– Range of machine sizes and capabilities
– Quality certifications and processes
– Capacity for prototyping versus production runs
– Value-added services like secondary operations and assembly
The right partner will combine technical expertise with a commitment to quality and customer service, ensuring your precision components meet all requirements.
## The Future of Swiss Machining
As manufacturing demands continue to evolve, Swiss machining technology advances to meet new challenges:
– Integration of automation for higher productivity
– Development of even more precise machine tools
– Expansion of capabilities to handle larger workpieces
– Improved software for programming complex geometries
These innovations ensure that Swiss machining will remain at the forefront of precision manufacturing for years to come.